Robotic Limitations In Nike Sneaker Manufacturing: Challenges And Solutions
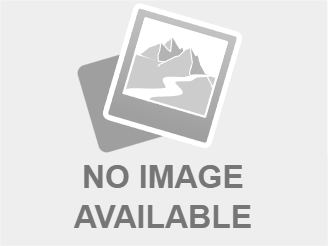
Table of Contents
The footwear industry, particularly giants like Nike, are increasingly exploring automation to improve efficiency and reduce costs. Robots offer significant potential in Nike sneaker manufacturing, promising faster production, higher consistency, and reduced labor costs. However, several limitations hinder their widespread adoption. This article explores these key challenges and investigates potential solutions, paving the way for a more automated future in sneaker production.
Dexterity and Precision Challenges in Complex Assembly
The intricate process of assembling a Nike sneaker presents significant dexterity and precision challenges for robots. Current robotic systems struggle to match the capabilities of human workers in several key areas.
Limitations of Current Robotic Grippers
Current robotic grippers often lack the dexterity needed to handle the diverse shapes, sizes, and materials used in sneaker assembly. This results in slower production speeds and increased error rates.
- Problem: Difficulty gripping delicate components like laces, thin fabrics, or intricate stitching. The varied textures and shapes make consistent gripping a challenge.
- Problem: Inconsistent gripping force can lead to damaged materials, wasted components, and production delays. Too much force can crush delicate parts; too little can result in dropped items.
- Solution: Developing more advanced grippers with adaptive pressure sensors and flexible fingers is crucial. Research into soft robotics, which utilizes compliant materials, offers promising advancements in this area. These soft grippers can conform to the shape of the object, improving grip and reducing damage.
Precision Issues in Glue Application and Stitching
Achieving the precise glue application and stitching needed for high-quality sneakers remains a significant hurdle. Human dexterity and fine motor skills surpass current robotic capabilities in these areas.
- Problem: Inconsistent glue distribution can lead to adhesion problems, affecting the structural integrity and longevity of the shoe. Precise, even glue application is critical for a strong bond.
- Problem: Inaccurate stitching can result in aesthetic imperfections and structural weaknesses. Consistent stitch length, tension, and placement are essential for quality and durability.
- Solution: Employing advanced vision systems for precise guidance and implementing AI-powered control systems for more accurate movements is necessary. Machine learning can help robots learn and refine their stitching and glue application techniques over time.
Adaptability and Flexibility in Variable Production Lines
Nike produces a vast array of sneaker models, each with its own unique design and assembly requirements. Adapting robots to this variable production environment poses significant challenges.
Programming and Re-programming Complexities
Re-programming robots for different sneaker models and production runs is a time-consuming and expensive process. This limits flexibility in adapting to changing consumer demands and fashion trends.
- Problem: High cost of reprogramming and the downtime required during changes significantly impact production efficiency and profitability. Each new model requires significant engineering and programming effort.
- Problem: Lack of adaptability to unforeseen variations in material or component properties can lead to production delays and errors. Slight variations in material thickness or texture can affect robotic performance.
- Solution: Developing more user-friendly programming interfaces and implementing AI-powered learning systems that allow robots to adapt to variations without extensive reprogramming is essential. Self-learning algorithms can help robots adjust to minor changes in materials or designs.
Integration with Existing Manufacturing Processes
Integrating robots into existing manufacturing lines can be complex and disruptive, requiring significant investment and downtime. Compatibility issues and workflow disruptions can hinder the adoption of automation.
- Problem: Compatibility issues between robotic systems and legacy equipment can slow down integration and increase costs. Older equipment may lack the necessary interfaces or communication protocols.
- Problem: Disruption to existing workflows during integration can lead to temporary production slowdowns and reduced efficiency. Careful planning and phased implementation are critical.
- Solution: Modular robotic systems designed for easy integration and backward compatibility with existing infrastructure are needed. Flexible and adaptable robotic solutions are key to seamless integration.
Cost and Return on Investment (ROI) Concerns
The high initial investment and ongoing maintenance costs associated with advanced robotic systems can pose significant barriers to adoption, especially for smaller manufacturers.
High Initial Investment Costs
The initial cost of purchasing and implementing advanced robotic systems, including robotic arms, grippers, sensors, and sophisticated software, can be prohibitive.
- Problem: High capital expenditure can deter smaller companies from investing in automation. The upfront costs can be substantial, requiring significant financial resources.
- Problem: The need for skilled technicians for installation, maintenance, and programming adds to the overall cost. Specialized expertise is required for effective operation and maintenance.
- Solution: Exploring leasing options or collaborative partnerships to reduce upfront costs can make automation more accessible. Focusing on cost-effective robotic solutions tailored to specific tasks can also improve ROI.
Long-term Maintenance and Repair Expenses
Maintaining and repairing complex robotic systems requires specialized expertise and can incur substantial ongoing expenses. Unexpected downtime due to malfunctions can further impact profitability.
- Problem: Unexpected downtime due to malfunctions can disrupt production and lead to lost revenue. Robust and reliable systems are critical to minimizing downtime.
- Problem: High cost of spare parts and specialized maintenance contracts adds to the long-term operational expenses. Preventive maintenance is crucial to extending the lifespan of the robots.
- Solution: Investing in robust and reliable robotic systems with built-in diagnostics and predictive maintenance capabilities can help minimize downtime and reduce maintenance costs. Developing partnerships with specialized maintenance providers can provide access to expertise and reduce costs.
Conclusion
While robotic limitations currently exist in Nike sneaker manufacturing, ongoing advancements in robotics, AI, and sensor technologies are providing promising solutions. Overcoming dexterity challenges, improving flexibility, and addressing cost concerns will be crucial for maximizing the benefits of automation in the footwear industry. By focusing on research and development in areas such as advanced grippers, AI-powered control systems, and modular robotic designs, the potential for significant improvements in Nike sneaker production efficiency can be realized. The future of Nike sneaker manufacturing depends on continued innovation and addressing the challenges of robotic integration to fully harness the potential of automation. Investing in research and development related to robotic limitations in Nike sneaker manufacturing is crucial for achieving optimal efficiency and competitiveness.
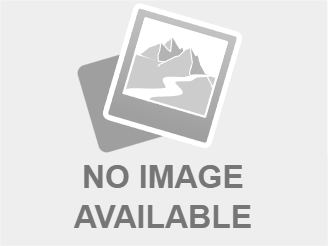
Featured Posts
-
Antitrust Scrutiny Intensifies Is A Google Breakup Inevitable
Apr 22, 2025 -
Will Google Be Broken Up Examining The Antitrust Challenges
Apr 22, 2025 -
Trump Administration To Slash Another 1 Billion In Harvard Funding
Apr 22, 2025 -
Metas Future Under A Trump Presidency Zuckerbergs Challenges
Apr 22, 2025 -
Is Google Facing Its Biggest Threat Yet A Potential Breakup Analyzed
Apr 22, 2025